Photo: Ark buildings are easily assembled by local workers, thus assisting developers achieve their local content objectives by providing training and employment for people in their footprint communities
Prefabricated modular building supplier, Ark Pacific, continues to increase its market share in the provision of camps across PNG’s resource sector. With a low freight footprint (up to 75 percent less) and proven commitment to quality and after sales service, Ark’s fit-for-purpose buildings are perfect for camps and a multitude of other building types required by mining and oil and gas operations.
Introduced to PNG during the LNG construction phase in 2010 for a 1,000 person multi-storey camp accommodation complex and office facilities, there are now thousands of Ark building modules around the country. Significantly, all of Ark’s buildings are assembled by local community workforces, thus helping developers achieve their local content objectives.
Ark has long-term building supply partnerships with several of its resource clients. General Manager, Cassius Ruka, who spent his childhood in PNG as well as most of his working life, knows the importance of building genuine client partnerships. Central to these partnerships is Ark’s commitment to after sales service and continuous quality improvement.
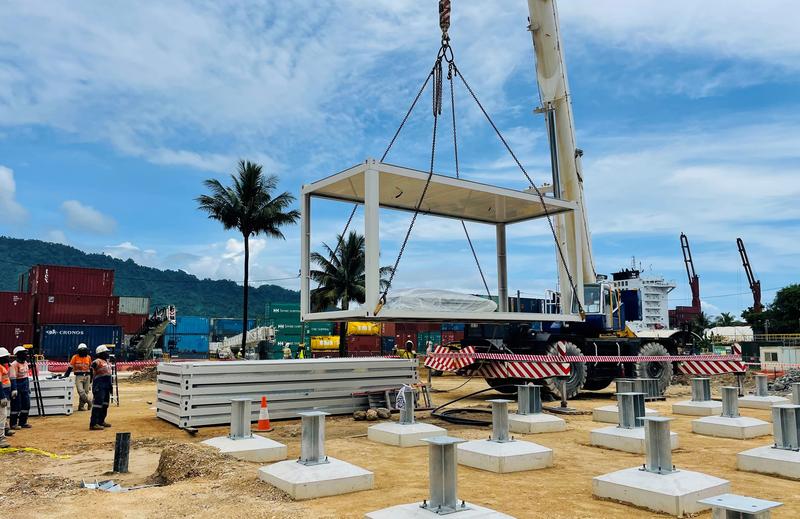
“We do whatever we can to make our buildings even better for our clients. Right now, Ark Pacific, is engaged in the process of working closely with one of PNG’s biggest mines to further improve the quality, design, constructability, and longevity of their buildings. This has involved carrying out inspections and conducting interviews with a range of stakeholders, including asset owners, construction project managers, maintenance coordinators, and facility end users. The data we’re gathering from this process will be used to develop an even better product, that is buildings that are increasingly fit for purpose, have enhanced longevity, and can accommodate the mine’s unique environmental factors and remoteness.”
Ruka is well versed in the challenges remotely located resource operations face when it comes to procuring camp accommodation and other buildings. “Irrespective of whether you’re an island operation like Lihir or a highland operation like Porgera, you need to be 100 percent certain that your buildings – which represent a major capex investment – are durable and can withstand whatever nature throws at them. Sulphur and salt, as well as excessive rain and moisture will all reduce building longevity. You also need to be able to get the buildings to site as easily and cost-effectively as possible which is incredibly difficult given remoteness combined with the state of our road network and current freight prices.”
Ark modular building units are engineered specifically for the harsh conditions of remote resource operations. Furthermore, clients can save up to 75 percent on their freight costs because Ark’s modular componentry is specifically engineered so that six of its flat pack units are equivalent to a single 20-foot shipping container when stacked together ready for transport. “In other words,” says Ruka, “instead of using five, six or seven trucks to get our units to the job site, the client only needs one.”
In addition to the low freight costs and durability associated with Ark Pacific’s prefabricated modular building systems, Ruka says his resource clients also benefit from:
- After sales services: Regular follow up and ongoing communication (i.e., not just from design through to handover, but for years afterwards).
- Quality guarantee: Cost of any defects 100 percent covered by Ark.
- Multiple configurations: Modules can be utilised for a multitude of building types and layouts (i.e., a range of ancillary buildings in addition to camps, such as offices, laboratories, messes, etc.,)
- Furniture and equipment supply: From office and bedroom furniture to commercial laundry and kitchen equipment.
- Local workforce assembly: Developer achieves local content objectives and local workers secure training and employment.
- Repurposability: Unbolt and disconnect the modules from one another to transport to another site and bolt them back together in a similar or different configuration.
- Buildings that ‘Give Back to PNG’: The repurposability of Ark buildings mean that they can be donated to footprint communities after they’re no longer needed by the developer.
To learn more about Ark Pacific, including its diverse range of fit for purpose camps and ancillary buildings, as well as the advantages of its unique building systems: www.arkpacific.net